智领未来ABB机器人软件助力高效智能工业升级
19429202025-03-25行业软件12 浏览
传统工业的智能化转型,是否只能依赖高成本与复杂技术?
在全球制造业加速向智能化迈进的今天,许多企业面临一个现实困境:如何在不牺牲效率与成本的前提下,实现生产流程的智能化升级?尤其是中小型企业,常因技术门槛高、投入成本大而望而却步。ABB机器人软件通过其创新功能与模块化设计,正在打破这一僵局。从汽车装配到精密电子制造,ABB的软件解决方案以高效、灵活、易用为核心,推动工业机器人从“机械臂”向“智能大脑”的转变。
1. 智能视觉系统:如何让机器人“看得清、抓得准”?
传统生产中的视觉盲区能否被消除?
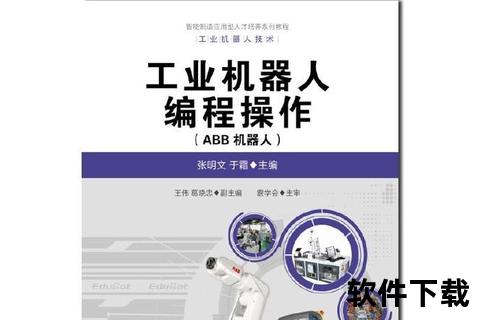
在复杂装配场景中,机器人对工件的精准识别与抓取是核心挑战。例如,某汽车零部件厂需根据法兰颜色自动匹配不同型号的关节基座,传统方案依赖人工调试和固定程序,效率低下且容错率低。而ABB机器人软件通过视觉检测模块与ProfiNET通信技术,实现动态调整与高精度操作。
以网页15中提到的视觉工作站为例,康耐视相机与ABB机器人协同工作时,通过智能算法对工件颜色、位置进行实时分析,并反馈至PLC和机器人主程序。机器人利用数组点位数据和偏移功能,快速生成抓取路径,将原本需要6个子程序的任务整合为1个参数化程序。这一改进使某工厂的装配效率提升30%,调试时间缩短50%。ABB的SmarTac接触传感器(网页14)通过软件集成,可在焊接前自动修正定位误差,将焊接起始点精度提升至±0.02mm,避免因工件偏移导致的废品。
2. 模块化编程:能否让机器人程序“一键适配多场景”?
臃肿代码如何简化为柔性化指令?
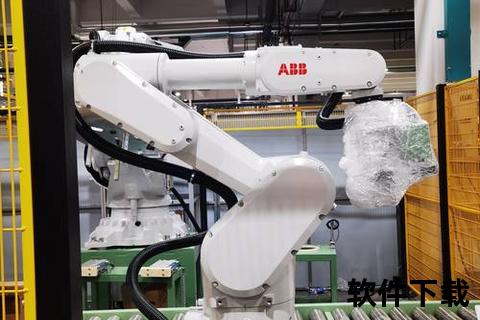
传统机器人编程常因场景变化需反复修改代码,导致程序臃肿且维护困难。ABB机器人软件通过模块化编程与低代码技术,将复杂指令转化为可复用的参数化模块。
例如,网页15描述的关节部件装配任务中,机器人需根据视觉反馈切换工具并抓取不同颜色工件。传统方案需为每种工具编写独立子程序,而ABB通过带参子程序与TEST...CASE指令,仅需1个主程序即可控制弧口工具、吸盘等多种工具的动作逻辑。这种设计使某电子制造商的产线切换时间从2小时缩短至15分钟。
ABB的RobotStudio云端版(网页65)支持远程协作与虚拟调试,工程师可通过AI生成程序框架,并实时优化路径规划。例如,秘鲁亚马逊雨林的种子播种项目中,位于瑞典的工程师通过云端软件远程控制YuMi协作机器人,完成高精度播种任务,验证了跨时区协作的可行性。
3. 云端协作与AI学习:机器人能否“自主进化”?
动态环境中的自主决策能否实现?
在物流分拣、柔性制造等场景中,机器人需应对不断变化的工件类型与生产需求。ABB软件通过AI学习与云端数据整合,赋予机器人自适应能力。
以网页65中提到的AI视觉焊接为例,机器人结合机器学习算法,可自动检测焊点缺陷,识别速度比人工快5倍,准确率达99.8%。某新能源汽车厂商采用此方案后,焊接废品率降低60%。而在仓储场景中,ABB的自主移动机器人(AMR)通过视觉与AI路径规划,可在动态环境中避障并优化运输路线,使某物流中心的吞吐量提升40%。
更值得关注的是,ABB的OmniCore控制器(网页65)搭载TrueMove运动控制技术,使新一代机器人IRB 6710系列在点焊、铆接等任务中重复精度达0.03mm,能耗降低20%。这一技术已应用于长城汽车等企业的冲压线,实现高质量装配与节能双赢。
智领未来!从技术到实践的落地建议
ABB机器人软件助力高效智能工业升级的案例表明,智能化转型并非遥不可及。企业可采取以下策略:
1. 引入智能视觉系统:优先部署视觉检测与动态路径规划,解决复杂抓取与装配难题。
2. 采用模块化编程:通过参数化设计与低代码平台简化程序维护,提升产线柔性。
3. 部署云端协作平台:利用RobotStudio等工具实现远程调试与AI优化,降低对专业技能的依赖。
正如ABB机器人业务全球总裁马思康所言:“未来的自动化是灵活、易用且可持续的。”通过软件与硬件的深度融合,智领未来!ABB机器人软件助力高效智能工业升级,正为全球制造业开启一条低门槛、高回报的智能化之路。