智能革新西门子仿真软件引领未来工业模拟新境界
19429202025-03-22驱动下载15 浏览
智能革新西门子仿真软件引领未来工业模拟新境界
你是否想过,工业设计中的“试错”成本究竟有多高?传统仿真工具耗时数月才能验证的模型,是否正在拖慢创新速度?在智能制造时代,工程师们需要的不仅是精准的模拟结果,更是跨越物理与数字鸿沟的协同能力。西门子以智能革新为引擎,正重新定义工业仿真的边界——从云端协作到人工智能辅助,从多物理场耦合到全生命周期管理,一场颠覆性的技术革命正在发生。
1. 云端协作能否打破物理界限?
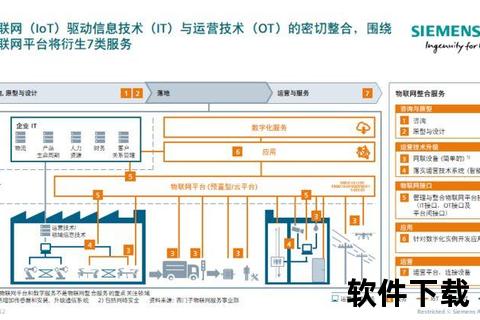
在传统工业仿真中,数据孤岛和硬件限制常导致协作效率低下。例如,某汽车制造商曾因全球团队无法实时共享仿真模型,导致新车研发周期延长了6个月。智能革新西门子仿真软件引领未来工业模拟新境界,其推出的Solid Edge X通过SaaS云平台解决了这一痛点。该平台支持多人在线协同设计,即使面对500GB的超大装配体数据,也能实现秒级加载和实时更新。
以西门子与某新能源电池企业的合作为例,工程师在德国修改电芯结构,中国团队同步优化散热仿真,美国团队则通过云端直接验证生产可行性。这种“零时差”协作将开发周期压缩了40%,并降低了30%的IT运维成本。云原生架构不仅打破了地域限制,更通过内置的Teamcenter数据管理,确保每个版本变更都被精准追溯,避免“版本地狱”问题。
2. AI能否让机器学会自我优化?
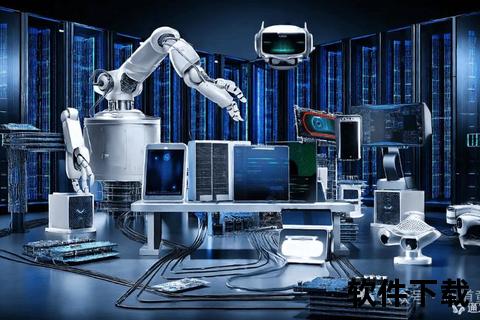
人工设置仿真参数如同大海捞针,而AI正在将这一过程转化为精准导航。西门子Simcenter 3D 2025版本引入的AI辅助功能,可在转子动力学分析中自动识别临界转速偏差。某航空发动机厂商使用该功能后,非线性振动分析时间从72小时缩短至4小时,同时将叶片断裂风险预测准确率提升至98%。
更突破性的案例来自西门子PAVE360汽车数字孪生平台。当某车企研发自动驾驶系统时,AI驱动仿真引擎在AWS云上并行运行了10万次极端场景测试——包括暴雨中的传感器失效、零下40℃的电池性能衰减等传统方法难以覆盖的工况。通过机器学习生成的“虚拟路测”数据,企业将实车验证成本降低了1700万美元。智能革新西门子仿真软件引领未来工业模拟新境界,在这里,AI不仅是工具,更是能自主进化的问题解决者。
3. 多物理场仿真能否终结复杂系统盲区?
当飞机机翼需要同时满足气动、结构、热力学要求时,单一物理场仿真就像盲人摸象。西门子与Altair的合作给出了答案:通过Simcenter与Inspire的深度集成,工程师可在统一平台完成颤振分析与拓扑优化。某国产大飞机项目应用该方案后,机翼减重15%的颤振临界速度提升了22%,这正是多物理场耦合仿真的威力。
在半导体领域,这种整合更具颠覆性。某芯片封装企业使用西门子Simcenter 3D的电磁-热耦合仿真,提前6个月预判了5nm芯片的散热瓶颈。通过动态模拟10亿个晶体管的功耗分布,他们优化了微通道冷却结构,使芯片峰值温度下降34℃。智能革新西门子仿真软件引领未来工业模拟新境界,意味着任何复杂系统都不再存在“未被计算的风险”。
让未来从仿真中生长
对于企业而言,拥抱这场变革需要三步走:
1. 构建混合云架构——将核心数据保留在本地,非敏感仿真任务迁移至云端,平衡安全与效率
2. 培养“仿真+AI”复合团队——建议工程师掌握Python数据分析和AI模型调优基础,例如通过西门子官方认证课程提升技能
3. 建立跨学科验证流程——参考航空航天业的“V型开发模型”,在需求阶段就规划多物理场验证节点
当数字孪生从概念走向生产一线,当AI开始自主推演千万种可能性,工业创新的游戏规则已被改写。西门子用智能革新证明:仿真不再是设计的后置校验,而是驱动创新的核心引擎。这或许正是未来工业最激动人心的新境界。
--