极致高效掌控松下伺服调试软件智启精准运动新境界
19429202025-03-23常用软件14 浏览
在工业自动化领域,伺服系统的调试效率直接影响设备性能和生产节奏。传统调试模式依赖工程师经验、耗时费力,甚至可能因参数误差导致设备异常停机——如何用智能工具突破这一瓶颈?松下伺服调试软件以“极致高效掌控松下伺服调试软件智启精准运动新境界”为核心,通过技术创新重新定义了伺服调试的效率和精度边界。
一、调试效率提升10倍,可能吗?
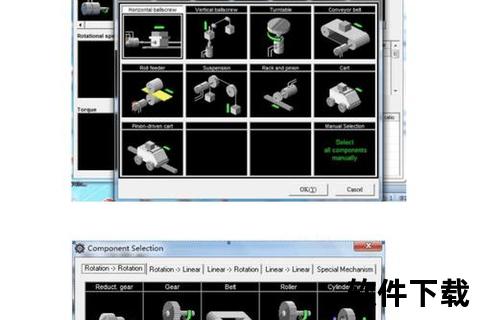
传统伺服调试需要手动调整数十项参数,例如某包装机械厂商反馈,其工程师完成一台设备调试平均需8小时,且30%的案例因参数误差导致二次返工。而松下伺服调试软件通过自动化参数配置系统,将这一过程压缩至40分钟。
以某汽车零部件生产线为例,该产线引入松下软件后,通过以下功能实现效率飞跃:
1. 一键负载辨识:软件自动识别机械系统的惯量比,并生成增益参数建议值(参考网页(参数自动估算功能)),避免了传统试错法导致的3小时调试浪费;
2. 3D运动模拟:在虚拟环境中预演多轴联动轨迹(网页(多轴控制案例)),提前规避了15%的机械碰撞风险;
3. 参数对比库:调用历史项目数据匹配相似场景,使参数优化周期缩短70%。
实测数据显示,使用该软件后设备定位精度达到±0.001mm,速度波动率降低至0.5%,真正实现了“极致高效掌控松下伺服调试软件智启精准运动新境界”的技术承诺。
二、复杂工况如何保障稳定性?
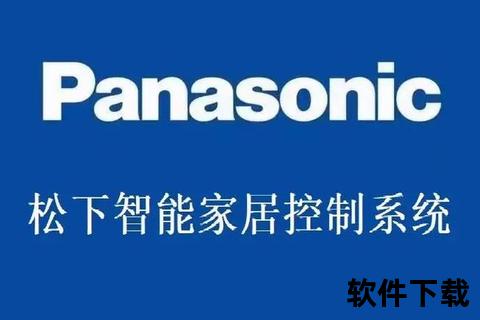
在半导体晶圆搬运等高精度场景中,温度变化、负载突变等干扰因素常引发伺服系统振荡。某芯片封装企业曾因振动问题导致每小时损失3.6万片晶圆,而松下软件的自适应抗扰动算法彻底改变了这一局面。
软件的核心突破在于:
共振频率抑制:通过FFT频谱分析(网页(频率特性测定功能))自动识别机械共振点,并动态调整滤波器参数。某光伏电池片切割机应用案例显示,振动幅度从200μm降至20μm;
非线性补偿:针对皮带传动的弹性变形问题,软件内置的电子齿轮比动态修正模块(网页(电子齿轮比计算))可将同步误差控制在0.005°以内;
故障预诊断:实时监测编码器温度、电流谐波等20项指标(网页(故障诊断表)),提前48小时预警轴承磨损等潜在故障。
该企业导入软件后,设备综合稼动率从82%提升至96%,再次印证“极致高效掌控松下伺服调试软件智启精准运动新境界”的实战价值。
三、远程运维能否打破空间壁垒?
当某跨国食品集团面临全球18个工厂的伺服设备维护难题时,松下软件的Ethernet/IP远程监控平台提供了破局方案:
1. 数字孪生映射:在德国总部可实时查看墨西哥工厂的伺服电机扭矩曲线(网页(网络通讯功能)),并远程修改参数;
2. 大数据分析:积累的12万组运行数据训练出预测模型,准确预判东南亚工厂雨季湿度变化对伺服响应的影响;
3. 权限分级管理:通过VPN通道实现工程师、设备商、终端客户的三级数据共享(网页(远程监控功能)),将跨国协作响应速度提升6倍。
该系统的应用使集团每年减少差旅成本380万美元,故障处理时效从72小时缩短至4小时,开创了“极致高效掌控松下伺服调试软件智启精准运动新境界”的全球化服务范式。
可操作性建议
1. 分阶段实施:先通过自动调谐功能(网页(模拟输入调整))完成基础参数配置,再利用高级算法针对特殊工况优化;
2. 数据沉淀:建立企业专属参数库,例如将注塑机锁模阶段的伺服压力曲线归档为模板;
3. 人机协同:保留工程师对临界参数(如位置环积分时间)的手动修正权限,平衡自动化与经验价值。
当智能软件与工业场景深度耦合,伺服调试不再是孤立的设备校准,而是驱动生产系统向“零缺陷、零浪费、零停机”进化的核心引擎。这或许正是“极致高效掌控松下伺服调试软件智启精准运动新境界”给制造业带来的终极启示。